Zhengzhou Huahong Machinery Equipment Co., Ltd.
Company Profile. Zhengzhou Huahong Machinery Equipment Co., Ltd. Zhengzhou Huahong Machinery Equipment Co., Ltd. is located in Zhengzhou National Hi-Tech …
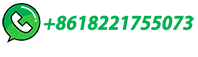
Company Profile. Zhengzhou Huahong Machinery Equipment Co., Ltd. Zhengzhou Huahong Machinery Equipment Co., Ltd. is located in Zhengzhou National Hi-Tech …
Our ball mill grinder is a versatile tool designed for grinding and blending materials into fine particles. Its cylindrical chamber houses the grinding medium—be it metallic or ceramic balls—allowing for smooth, efficient milling. Widely used in industries such as mining, ceramics, and pharmaceuticals, this grinder operates through rotation ...
I prepared FeCoNiAlMn and FeCoNiAlMn1-xCrx (x=0.2,0.4,0.6, 0.8,1) using Ball mill with 45hrs milling but for increasing the crystallinity of my powder alloy samples I need to heat them in vacuum ...
The Wet Milling Method: A Deep Dive. Wet milling, a core aspect of the wet grinding process, involves breaking down materials in a liquid medium. The wet ball milling process, a popular choice in many sectors, employs a ball mill to achieve a fine grind. This method is particularly effective for materials that are too hard for standard milling ...
The effect of ball size on the particle size reduction has been investigated first for varying rotation speed of the container. Percent passing and size distributions of the milled Al 2 O 3 powder are shown in Fig. 1, Fig. 2, respectively, as a function of particle size for varying ball size.The average particle sizes (d 50) of the milled Al 2 O 3 powder are …
Yttria-reinforced copper matrix composites were prepared by dry ball milling (DBM) and wet ball milling (WBM), respectively, followed by spark plasma sintering …
The effect of ball-milling speed on the electrochemical performance is also investigated. The composite, fabricated at a high ball-milling speed of 1500 rpm, shows a better dispersion of sulfur and superior cycle stability, but very low sulfur utilization due to the damage of cross-linked conductive carbon matrix. All these findings can offer ...
Ball milling is one of the few unit operations that actual improve in performance and efficiency with increasing size. The ABBE Slice Mill is the same as the product mill and can replicate all mill operating parameters …
Results: Comparable particle sizes of about 151 nm to 190 nm were obtained for both active pharmaceutical ingredients at the same milling time and milling speed when the drugs were processed at 10 g using low energy wet ball milling or 120 g using high energy wet ball milling in batch mode, respectively. However, an adjustment of the milling ...
At Economy Ball Mill, we've seen a growing interest in wet grinding processes, and for good reason. Wet grinding is a powerful and efficient material …
After 5 min ultrasonication, the obtained suspension was ground by a ball mill in a zirconia vial with zirconia balls (0.8 mm) to form a homogeneous suspension. Detail of the wet ball-milling have been described previously [31], [32]. The mass ratio of zirconia balls to the whole raw material was maintained at 20:1 and the mixture was …
Traditional Wet Milling. The coatings industry is no different from others in its search for modern manufacturing techniques. The traditional high-speed dissolver, ball mill, vertical mill and standard …
Wet ball milling can be used to grind a wide range of materials, including ceramics, minerals, metals, and polymers. It can also be used for the synthesis of materials, such as nanoparticles, and the modification of surfaces. Applications of Wet Ball Milling. Wet ball milling has found numerous applications in various industries.
A novel environmentally-friendly parametric modeling of wet ball-milling- Na 2 CO 3 (aq) leaching at low temperature without roasting operation was carried out to recover vanadium from vanadium-bearing steel slag (VBSS). The paradigm shift in the source of strategic metals (SMs) globally validates the fact that the gangue of today is …
The wet ball mill has a simple transportation device with less auxiliary equipment, so the investment is about 5%-10% lower than that of a dry ball mill. The grinding particle size is fine and uniform. The wet ball milling can not only grind agglomerate into fine particles, but also mix the lean material and the plastic material …
The Effect of Aluminium and Wet High Energy Ball Milling on the Properties and Composition of SiC. AMI: Materialia. 20 Pages Posted: 1 Oct 2024 Publication Status: Under Review. See all articles by Sarah Morais Bezerra ... This study combines high-energy ball milling, combustion synthesis, and the addition of an initiator to investigate their ...
The Wet Milling Method: A Deep Dive. Wet milling, a core aspect of the wet grinding process, involves breaking down materials in a liquid medium. The wet ball milling process, a popular choice in many sectors, …
WET BALL MILL OF FLEXIBLE BASE TXDOT DESIGNATION: TEX-116-E CONSTRUCTION DIVISION 2 – 4 EFFECTIVE DATE: APRIL 2024 REVIEW DATE: APRIL 2024 PART I—WET BALL MILL PERCENT 3. PROCEDURE 3.1 Sample flexible base material in accordance with Tex-100-E. 3.1.1 Split or quarter the sample in accordance …
Yttria-reinforced copper matrix composites were prepared by dry ball milling (DBM) and wet ball milling (WBM), respectively, followed by spark plasma sintering (SPS). It is to determine which milling process is better for fabricating Cu–Y2O3 composites. It is found that Cu–Y2O3 composites synthesized by DBM exhibit better densification, …
Wet Ball Mill. Wet type ball mill are mostly used in the industry production. It is to increase the high grinding efficiency under the ball mill grinding and striking, from which the …
A wet-rotating disc milling was used as a method to prepare ceramic slurry. The rheological measurements of the milled slurries showed that the apparent viscosity of the wet-rotating disc milled slurry was low and the slurry was nearly Newtonian behavior, whereas that of ball-milled slurry was more viscous and the slurry exhibited a very …
Wet ball milling is more adept at generating smaller and dispersed biochar particles than dry ball milling [31]. Wet ball milling composite of ZVI and Fe 3 O 4 showed a splendid synergy in electron storage and electron transfer [32]. The sulfide solution is effective in minimizing ZVI oxidation during wet milling [14].
A wet ball milling route was used to synthesise SiC-graphene core-shell nanoparticles in situ from graphite and SiC nanoparticles. Graphite flakes were gradually exfoliated into fresh graphene nanosheets (GNSs) without significant defects, which is attributed to mechanical shearing and moderate impaction forces between graphite …
If the rate of feed increased, coarser product will be obtained and if speed of rotation is increased the fineness for a given capacity is increases. During grinding, the balls themselves wear and are continuously replaced by new ones so that mill contains balls of various ages. Ball mill produces 1 to 50 ton/hr of powder and energy requirement ...
PQ-N4 series planetary ball mills may be used for mixing, homogenizing, fine grinding, mechanical alloying, cell disruption, small volume high-tech material production and even colloidal grinding. They are the ideal wet/dry milling tools for acquiring research samples with high efficiency and low noise. Vacuum jars may be used to process sample within a …
[Ball Mill of 1-50 TPH] Drop your whatsapp number for cost and more details. We offer technical guidance and free installation for customers. Applied material: gold ore, kaolin, limestone, plaster, copper, lead-zinc, iron ore, clay, cement, etc.
Established in early 1994, YUANREN is one of the most professional wet ball mill manufacturers and suppliers in China. Please rest assured to buy high quality wet ball …
Qym1510 Grinding Machine. ... Wet Ball Mill Cup Publishing In Malaysia Price. ... China Manufacturer.This page is about the grinding mill,includes micro powder mill,high pressure mill,ygm model,raymond mill,3r,4r,5r,6r and ball mills,if you want to buy these joyal grinding mills,you can contact us!
The ball milling process is divided into dry and wet milling processes according to the wettability factor. In dry milling, the particulates' erosion occurs through …
Wet Ball Mill. Wet ball grinder is a key equipment for grinding materials after crushing. Product Specification: φ900×1800-Φ2200×7500. Product Output: 0.65-2t/h-15-30t/h. Application Fields: Various ores and other …
حقوق النشر © 2024.Artom كل الحقوق محفوظة.خريطة الموقع